Category: Industry Information
Date: 2018-07-13
Click: 5783
Author: admin
Collection:
Experiments have shown that while the battery is heated to the melting point of the wax, the lithium ion battery has an internal short circuit and the battery temperature rises rapidly [5].
The safety of the power battery during use is our first consideration. Therefore , we have also established a strict safety assessment system for the evaluation of power batteries , such as extrusion, acupuncture, overcharge, over discharge and short circuit. , respectively, to simulate the abuse encountered by lithium-ion batteries in actual use . Among all the security issues, one is the most difficult to simulate - an internal short circuit. As the name suggests, internal short-circuit refers to the presence of excess material in the battery due to defects in the design or manufacture of lithium-ion batteries, or lithium dendrites, which cause damage to the diaphragm , where a short circuit between the positive and negative electrodes occurs, which is the most dangerous. In this case, because the energy of the entire battery is released through this short-circuit point (up to 70% of the energy will be released within 60s [1]), so the temperature here rises rapidly, and then the positive and negative active substances are triggered. , electrolyte by decomposition, thermal runaway caused by a lithium ion battery.
Since the short circuit occurs inside the lithium ion battery, it is difficult to simulate the damage caused by the internal short circuit by external action. For example, a common acupuncture experiment, in the process of needle penetration, a short circuit occurs at a point first, but with The needle is inserted into the inside of the battery. At this time, multiple short-circuits occur in the battery at the same time, so that the current density is greatly reduced. In addition, the needle also takes away some of the heat generated by the short circuit. Therefore, the needle test is simply "compared to the internal short circuit". Too gentle."
During the extrusion test, as the deformation of the battery increases, the diaphragm mechanically fails, causing a short circuit inside the battery, but the short-circuit point caused by the extrusion generally has a large area, or multiple points are simultaneously short-circuited, so Short-circuit current caused by the extrusion test is also greatly reduced [2], so the extrusion test cannot perfectly simulate the short circuit in the lithium-ion battery.
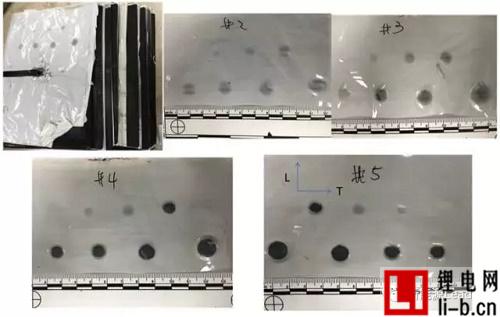
It can be seen that the common safety test method does not simulate the internal short circuit of the lithium ion battery, or the evaluation standard is not strict enough. Whether it is the extra material introduced in the production process or the lithium dendrites generated during the process, in essence, the short circuit inside the lithium ion battery is caused by the excess inside the battery core (especially the conductive excess). According to this, the Japanese Battery Association proposed a method for simulating a short circuit in a lithium ion battery. After the battery core is taken out, a small piece of metal is placed inside the battery core, and then placed in the battery case, and finally the battery is Put it into the extrusion equipment and apply pressure to the battery until the battery is short-circuited. The method can accurately simulate the situation of internal short circuit of the lithium ion battery, but since the method needs to disassemble the battery, the method is rarely used to evaluate the battery in actual production.
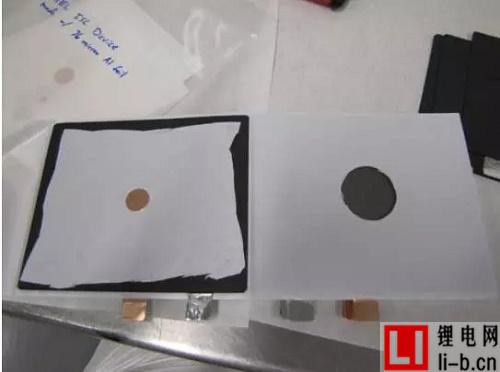
Other methods that can simulate a short circuit in a lithium-ion battery, most of which also require the introduction of excess material inside the battery, such as Sandia National Laboratory to introduce Wood's metal (the metal melting point is only 70 degrees Celsius) excess in the battery. The National Renewable Energy National Laboratory NREL simulates a short circuit in a lithium-ion battery by introducing a phase change material into the cell. In general, these methods need to open the battery and introduce excess material, so it is lack of operation in practical applications. Sex [3].
In order to solve the practical problem, the traditional extrusion test parameters of Wei Cai et al. [4] of Oak Ridge National Laboratory were optimized to produce a diameter of 1- between the two electrodes inside the lithium ion battery. 2mm short-circuit point, and can produce short-circuit points of different sizes by adjusting the experimental parameters. The experimental mode is shown in the figure below.
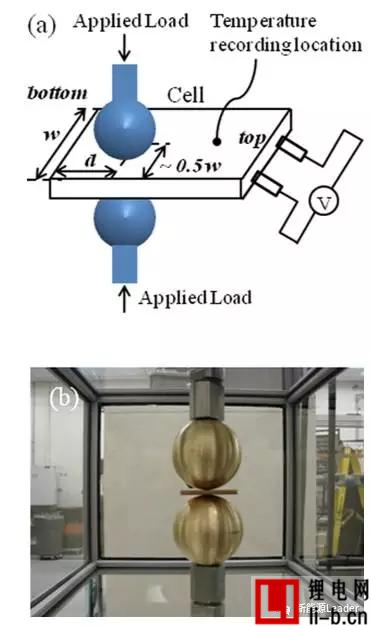
The key to the internal short-circuit simulation method proposed by Wei Cai et al is the timing of stopping the extrusion. The following figure is a picture of stopping the extrusion when the battery voltage drops to 1.0V (top) and 3.0V (bottom) respectively. After the battery voltage drops to 1.0V, the hole through which the diaphragm is burned through is significantly larger. When the 3.0V is cut off, the hole through which the diaphragm is burned through is about 1-2 mm, which is closer to the size of the short circuit point in the actual internal short circuit. The main advantage of this method is to simulate the short circuit inside the lithium ion battery without destroying the battery, which greatly improves the practicability of the method.
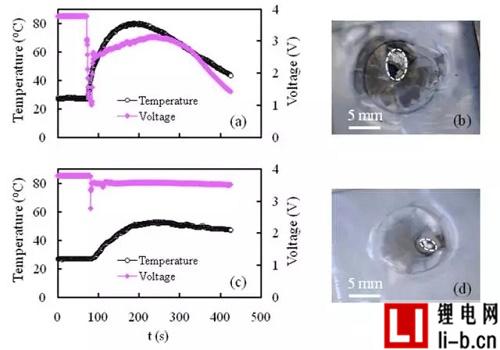
In order to more accurately simulate the occurrence of short circuit in lithium ion batteries, a wax-based internal short circuit device has been developed. The melting point of wax is only about 57 °C, so it is only necessary to heat the lithium ion battery to a very low temperature. After melting, the internal short circuit of the lithium ion battery can be induced. Experiments have shown that while the battery is heated to the melting point of the wax, the lithium ion battery has an internal short circuit and the battery temperature rises rapidly [5]. The biggest advantage of this method is that it can restore the true internal short circuit of the lithium ion battery to the utmost extent, and the method also has the characteristics of simple and easy operation. It is only necessary to add the device in the battery core when manufacturing the lithium ion battery. , greatly improving the practicality of the method. Especially in the case of short circuit in a battery in an analog battery pack, this method is almost the only feasible simulation method at present.
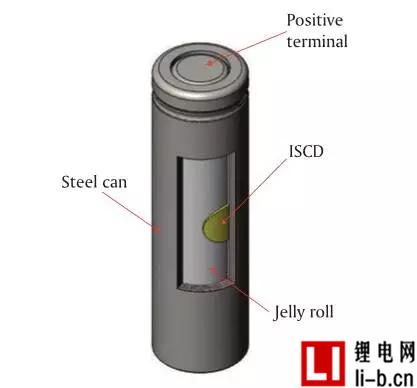
Excessive substances, lithium dendrites, etc. inside the lithium ion battery due to manufacturing defects or design defects are the most common causes of internal short circuits in lithium ion batteries, such as the Boeing 787 Dreamliner lithium ion battery fire incident in Boston. The letter is caused by lithium dendrites generated by lithium ion batteries charging at low temperatures, resulting in internal short circuits. With the popularity of electric vehicles , similar security incidents will continue to occur. How to reduce the loss caused by lithium-ion batteries in the event of internal short circuit is a problem that our lithium-ion battery designers need to consider, so for lithium-ion batteries The simulation of internal short circuit becomes more important. In light of the above introduction, Xiaobian believes that wax-based internal short-circuiting equipment (ISCD) is a more feasible method. This device can be added in the process of lithium-ion battery production, only need to be lithium ion. The lower temperature of the battery can induce the internal short circuit of the lithium ion battery, so it is very practical, especially when an internal short circuit occurs in a battery in the analog battery pack, this method is almost the only feasible method.